The rhythmic hum of a compressor, often overlooked in the symphony of our daily lives, plays a critical role in countless applications. From keeping our homes cool on sweltering summer days to powering industrial machinery, these workhorses silently toil away. But what happens when this rhythmic hum falters, replaced by a disconcerting silence or an unfamiliar clatter? How do you troubleshoot a defective compressor and restore its vital function?
This comprehensive guide will equip you with the knowledge and skills to diagnose and address compressor issues, empowering you to tackle these mechanical beasts with confidence.
Identifying Signs of Compressor Failure
Before delving into the intricacies of troubleshooting, it’s crucial to recognize the telltale signs of a failing compressor. Early detection can prevent further damage and costly repairs. Keep a keen eye out for these warning signs:
- Diminished Performance: A noticeable decrease in the compressor’s output, such as reduced cooling capacity in an air conditioner or lower air pressure in an air compressor, is often the first indication of trouble brewing.
- Unusual Noises: A healthy compressor operates with a consistent hum. Grinding, squealing, knocking, or rattling sounds emanating from the unit signal potential internal damage and warrant immediate attention.
- Frequent Cycling: If your compressor cycles on and off more frequently than usual, it could indicate a problem with its internal components or an issue with the system it serves.
- Tripped Circuit Breakers: Repeated tripping of circuit breakers or blown fuses connected to the compressor point towards an electrical fault within the unit, potentially a motor issue.
- Overheating: Excessive heat emanating from the compressor, beyond its normal operating temperature, suggests internal problems, possibly due to inadequate lubrication or a failing motor.
Understanding the Different Types of Compressors
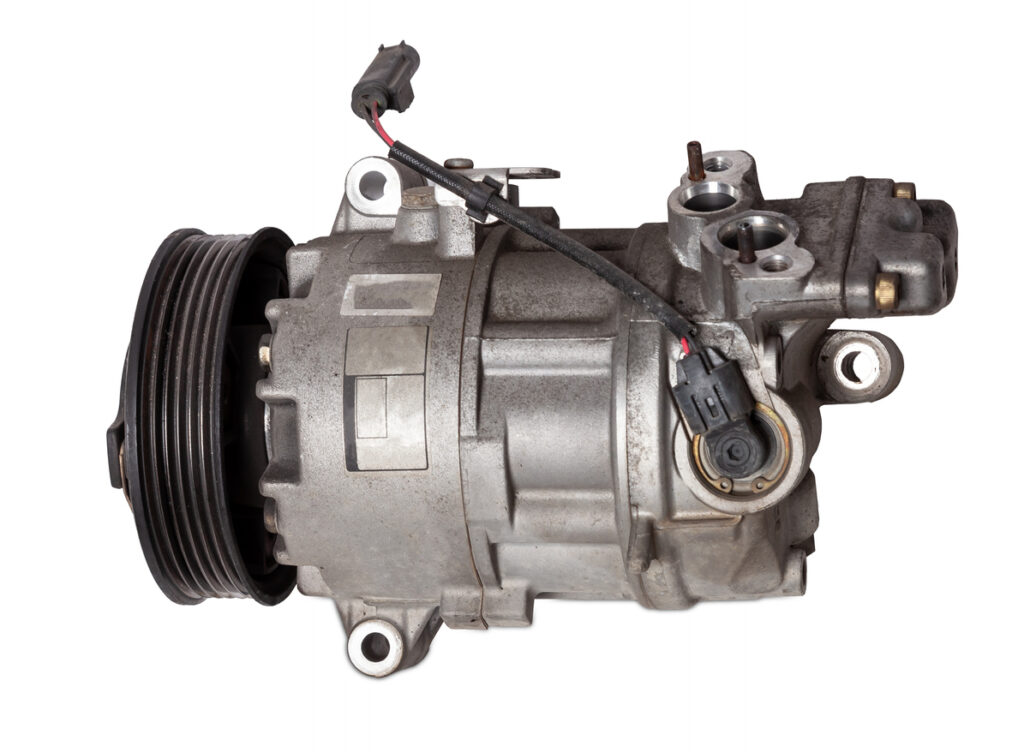
Compressors, like the diverse orchestra of the mechanical world, come in various types, each with its unique characteristics and potential failure points. Understanding these distinctions is crucial for effective troubleshooting.
1. Reciprocating Compressors: These workhorses utilize a piston-cylinder arrangement to compress air or refrigerant. Common issues include worn piston rings, faulty valves, and leaking gaskets.
2. Rotary Screw Compressors: Employing two helical screws to compress air, these are known for their quiet operation and efficiency. Potential problems include worn bearings, rotor damage, and lubricant degradation.
3. Centrifugal Compressors: These units utilize a high-speed impeller to impart velocity and pressure to the gas. Common issues involve impeller imbalance, bearing wear, and seal failures.
4. Scroll Compressors: Known for their smooth and quiet operation, these compressors use two spiral-shaped scrolls to compress refrigerant. Potential problems include scroll wear, motor failure, and refrigerant leaks.
Check for Power Supply Problems
Before dismantling the compressor, ensure it’s receiving adequate power. A simple oversight can save you hours of unnecessary troubleshooting.
- Inspect the Power Cord: Examine the power cord for any visible damage, such as cuts, frays, or burns. Replace a damaged cord immediately.
- Verify Voltage Supply: Using a multimeter, check the voltage at the compressor’s power terminals. Ensure it matches the unit’s specifications.
- Test the Circuit Breaker: Reset any tripped circuit breakers and replace any blown fuses. If the issue persists, it indicates a potential short circuit within the compressor.
Assess the Refrigerant Levels in the System
For compressors used in cooling applications, refrigerant acts as the lifeblood of the system. Insufficient refrigerant levels can lead to reduced performance and compressor damage.
- Check for Leaks: Visually inspect the refrigerant lines for any signs of oil residue, which can indicate a refrigerant leak.
- Measure Refrigerant Pressure: Using a manifold gauge set, measure the refrigerant pressure on both the high and low sides of the system. Compare the readings to the manufacturer’s specifications.
- Address Leaks and Recharge: If a leak is detected, repair it before recharging the system with the appropriate type and amount of refrigerant.
Inspect Electrical Connections for Security
Loose or corroded electrical connections can disrupt the compressor’s operation and pose safety hazards.
- Tighten Connections: Ensure all electrical connections, including those at the compressor, motor starter, and control board, are secure and free of corrosion.
- Inspect Wiring Insulation: Examine the wiring insulation for any signs of damage, such as cracks or melting. Replace any damaged wiring.
Examine for Inadequate Lubrication
Proper lubrication is vital for smooth compressor operation and longevity. Insufficient lubrication can lead to excessive friction, wear, and premature failure.
- Check Oil Level: For oil-lubricated compressors, verify the oil level through the sight glass or dipstick. Maintain the oil level within the manufacturer’s recommended range.
- Inspect Oil Condition: Observe the oil’s color and clarity. Dark or milky oil indicates contamination and necessitates an oil change.
Look for Signs of Overheating
Overheating can significantly shorten a compressor’s lifespan and lead to catastrophic failure. Identify and address overheating issues promptly.
- Feel for Excessive Heat: Carefully touch the compressor’s exterior. While it’s normal for the unit to be warm during operation, excessive heat indicates a problem.
- Check Cooling System: For air-cooled compressors, ensure the cooling fins are clean and unobstructed. For water-cooled units, verify proper water flow and temperature.
- Investigate Internal Components: If overheating persists, internal components like the motor windings or bearings may be failing and require professional attention.
Listen for Unusual Noises from the Compressor
Unusual noises emanating from the compressor are often the first indication of internal problems. Pay close attention to these auditory clues.
- Grinding Noises: Grinding sounds usually indicate metal-to-metal contact, potentially due to worn bearings, a failing motor, or damaged internal components.
- Squealing Noises: High-pitched squealing often points towards a failing bearing or a loose belt.
- Knocking or Rattling Noises: These sounds suggest loose components, such as a loose piston pin, connecting rod, or crankshaft bearing.
Clean Dirty Condenser Coils
For compressors used in cooling systems, dirty condenser coils restrict airflow, reducing efficiency and leading to overheating.
- Inspect Condenser Coils: Regularly inspect the condenser coils for dirt, debris, or obstructions.
- Clean Coils Gently: Use a soft brush, compressed air, or a gentle stream of water to clean the coils carefully, avoiding damage to the fins.
Consider the Age and Condition of the Compressor
Like any machine, compressors have a finite lifespan. Age and wear can take their toll, making repairs less cost-effective.
- Evaluate Repair Costs: If the compressor is nearing the end of its expected lifespan, weigh the cost of repairs against the cost of a replacement unit.
- Consider Energy Efficiency: Newer compressor models often offer improved energy efficiency, potentially saving you money on operating costs in the long run.
Review Maintenance History for the Compressor
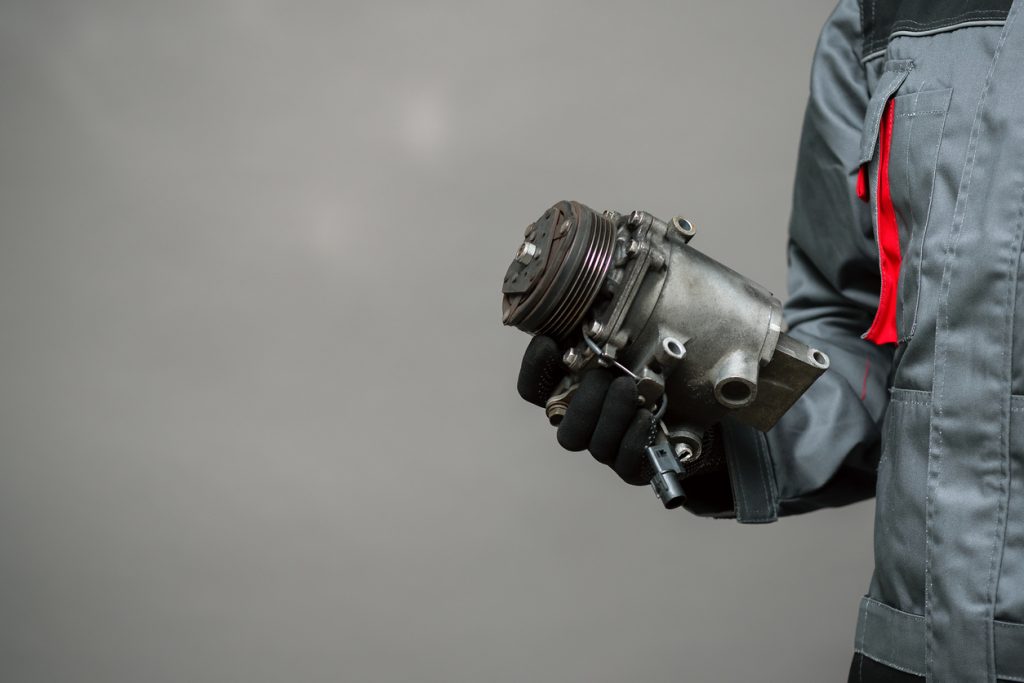
A well-documented maintenance history provides valuable insights into the compressor’s health and can aid in troubleshooting.
- Identify Recurring Issues: Review past maintenance records for any recurring problems, which can point towards a chronic issue.
- Assess Maintenance Practices: Evaluate the regularity and thoroughness of past maintenance practices. Inadequate maintenance can contribute to premature compressor failure.
Conclusion
Mastering the art of “how do you troubleshoot a defective compressor” empowers you to maintain these essential machines, ensuring their reliable operation and extending their lifespan. By understanding the compressor’s inner workings, recognizing warning signs, and employing systematic troubleshooting techniques, you can confidently address issues and keep these mechanical hearts beating strong.
ALSO READ: What Causes a Cracked Cylinder Head
FAQs
A: While it’s technically possible to repair a seized compressor, the extent of damage often makes replacement a more cost-effective solution.
A: The recommended service interval varies depending on the compressor type, usage, and operating environment. Consult the manufacturer’s guidelines for specific recommendations.
A: No, using the incorrect type of oil can damage the compressor. Always use the lubricant specified by the manufacturer.
A: Compressor lifespan varies depending on factors like type, usage, maintenance, and operating conditions. However, with proper care, many compressors can last 7-10 years or more.
A: Optimizing the compressor’s operating pressure, ensuring adequate ventilation, and addressing leaks can significantly improve energy efficiency.