When it comes to steel wire ropes, Italy stands out as one of the key players in the global market. Known for its engineering expertise and precision manufacturing, Italian steel wire rope products have become highly sought after for their reliability, durability, and performance across various industries.
If you’re considering sourcing steel wire rope from Italy, you’re likely looking for high-quality, durable options that can meet your project’s specific needs. Italian manufacturers have been producing steel wire rope for decades, gaining a reputation for reliability and innovation.
Importance of Wire Rope in Different Industries
Imagine constructing a towering bridge without reliable wire ropes or operating a mine without dependable cables. It’s unthinkable, right? Wire ropes are integral to the functionality and safety of numerous sectors.
- Construction Industry: From cranes lifting tons of steel beams to the hoists that move materials vertically, wire ropes are essential. They provide the strength and flexibility needed to handle heavy loads while maintaining safety standards.
- Maritime Sector: Ships rely on wire ropes for anchoring, mooring, and towing. The harsh marine environment demands ropes that can withstand corrosion and fatigue, a challenge that high-quality Italian steel wire ropes meet head-on.
- Mining Operations: Deep underground or high on the surface, mining equipment depends on wire ropes for hauling loads, operating lifts, and ensuring workers’ safety.
- Transportation: Elevators, cable cars, and even funiculars use wire ropes for smooth and secure operations, transporting people and goods efficiently.
- Entertainment and Sports: From zip lines to suspension in theatrical productions, the need for reliable wire ropes extends to leisure activities as well.
The reliability of these ropes directly impacts operational efficiency and safety. That’s why industries across the globe turn to steel wire rope from Italy, knowing they’ll get unmatched quality backed by a legacy of metallurgical expertise.
How to Select the Right Steel Wire Rope for Your Project?
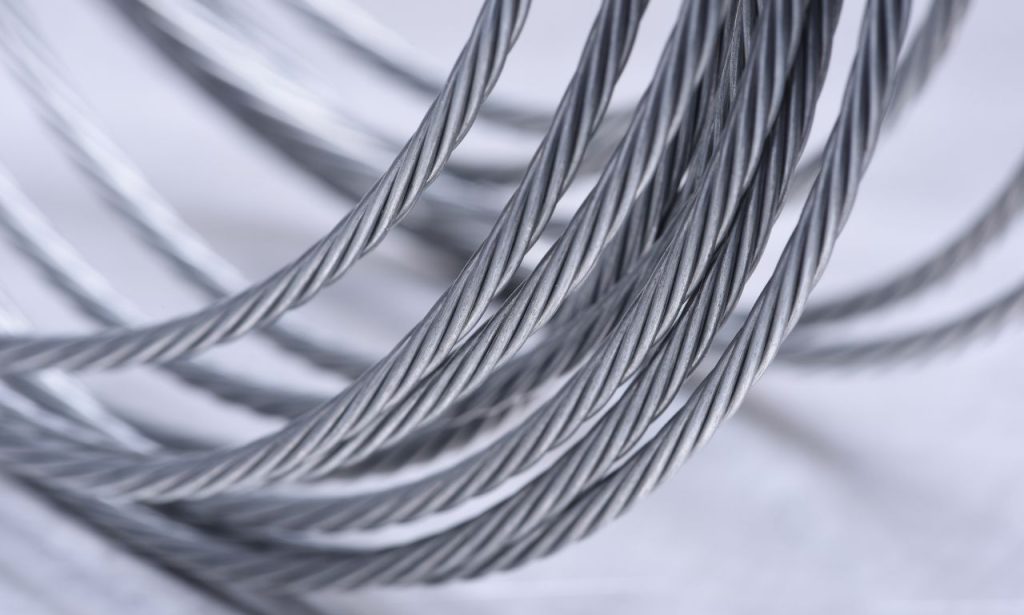
Choosing the right wire rope is crucial for safety and efficiency. Consider the following factors:
- Load capacity: Ensure the rope can handle the maximum weight it will be subjected to.
- Environment: Factor in exposure to moisture, chemicals, or extreme temperatures.
- Flexibility: Choose a rope with the appropriate flexibility for your application.
- Abrasion resistance: Select a rope with a durable coating for harsh environments.
By carefully evaluating these factors, you can select the ideal steel wire rope for your specific needs, ensuring optimal performance and longevity.
Certified Wire Rope Ferrules
Definition and Function
At first glance, ferrules may seem insignificant compared to the massive steel ropes they accompany. However, their role is critical. A ferrule is a metal sleeve, often made from aluminum, copper, or steel, used to form a loop at the end of a wire rope.
- Purpose: Ferrules secure the ends of wire ropes, preventing unraveling and providing an attachment point for hooks, shackles, or other hardware.
- Functionality: By compressing the ferrule onto the rope (a process known as swaging), it holds the rope’s strands together firmly.
- Application: Used in creating eye terminations, which are essential for connecting wire ropes to anchors, lifting devices, or other ropes.
Benefits for Safety and Performance
Using certified wire rope ferrules isn’t just about compliance; it’s about ensuring every component of your lifting or rigging system is up to the task.
- Safety Assurance: Certified ferrules have undergone rigorous testing to meet international standards. This certification guarantees that they can handle specified loads without failure.
- Optimal Performance: High-quality ferrules maintain the integrity of the wire rope. Improper or inferior ferrules can cause stress concentrations, leading to premature rope failure.
- Extended Lifespan: Certified ferrules contribute to the overall durability of the wire rope assembly. They prevent excessive movement of the strands, reducing internal wear.
In applications where human lives and significant investments are at stake, like in construction hoists or elevator systems, the use of certified components is non-negotiable. Italian manufacturers are known for producing ferrules that not only meet but often exceed international safety standards.
Mechanical Splicing
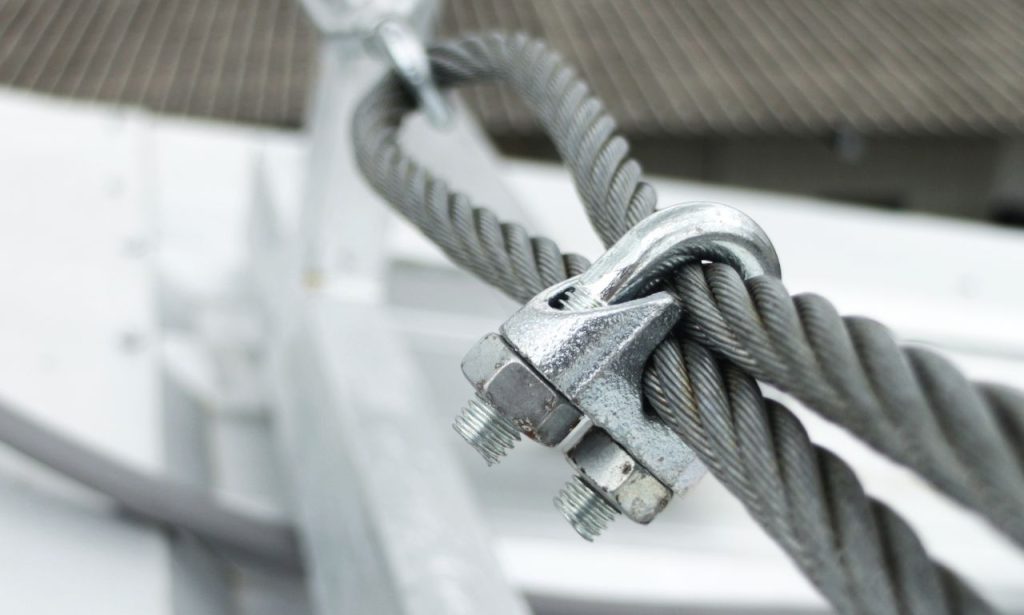
Overview and Techniques
Mechanical splicing is a method used to join two wire ropes or to create an eye (loop) at the end of a rope without compromising its strength.
- Process: The most common technique involves looping the rope back onto itself and securing it with a ferrule. This requires precise compression to ensure the splice can handle the intended load.
- Tools and Equipment: Swaging machines are used to compress the ferrule onto the rope uniformly. These machines apply high pressure to deform the ferrule material around the rope strands tightly.
- Types of Mechanical Splices:
- Return Loop: The rope end is bent back, and a ferrule is swaged to create a loop.
- End-to-End Splice: Two rope ends are joined using metal sleeves or connectors.
Advantages Over Traditional Methods
Mechanical splicing offers several benefits compared to other rope termination methods, such as knots or manual splices.
- Consistency and Reliability: Mechanical splices provide uniformity, which is crucial for load distribution. Knots can reduce the rope’s strength by up to 50%, while a properly made mechanical splice retains up to 95% of the rope’s strength.
- Time Efficiency: Mechanical splicing is quicker than manual splicing, which can be time-consuming and requires a high level of skill.
- Professional Finish: The result is a clean, smooth splice that minimizes snagging and is more aesthetically pleasing, which can be important in certain applications.
When utilizing steel wire rope from Italy, mechanical splicing ensures that the rope’s superior material properties are fully utilized without being compromised by inferior termination methods.
Selecting the Right Wire Rope
Application Considerations
Choosing the right wire rope is not a one-size-fits-all situation. The specific requirements of your application dictate the type of rope you need.
- Load and Strength Requirements: Calculate the maximum load the rope will need to handle, including any dynamic forces that could increase the strain.
- Environmental Conditions: Exposure to elements like saltwater, chemicals, or extreme temperatures can affect rope performance. For marine environments, for instance, galvanized or stainless-steel ropes offer better corrosion resistance.
- Flexibility vs. Strength: Some applications require highly flexible ropes (like those with more wires per strand), while others prioritize strength over flexibility.
Diameter and Construction Factors
Understanding rope construction is paramount.
- Diameter: The rope’s diameter affects its breaking strength and suitability for certain equipment, such as sheaves and drums.
- Strand Configuration:
- 6×19 Classification: Consists of 6 strands with 19 wires each. It’s a good balance of flexibility and abrasion resistance.
- 6×36 Classification: Has more wires per strand, offering greater flexibility but less resistance to abrasion.
- Core Types:
- Fiber Core (FC): Offers maximum flexibility but less strength and resistance to crushing.
- Independent Wire Rope Core (IWRC): Provides higher strength and resistance to heat and crushing.
Selecting a steel wire rope from Italy means you have access to a wide range of options, each manufactured with precision to meet specific needs.
The Role of Lubrication
Lubrication is a critical, yet often overlooked, aspect of wire rope maintenance.
- Reducing Internal Wear: Lubrication minimizes friction between individual wires and strands as the rope bends and moves during operation.
- Preventing Corrosion: Lubricants act as a barrier against moisture, chemicals, and other corrosive agents, extending the rope’s life.
- Ease of Handling: A well-lubricated rope is easier to handle and operates more smoothly, which is especially important in applications with repetitive movements.
Different applications may require specific types of lubricants. For example, ropes used in food processing facilities need food-grade lubricants. Italian wire ropes often come pre-lubricated with high-quality products suitable for various environments.
Transition to Acera HMPE Ropes
Comparison with Traditional Steel Wire Ropes
High-Modulus PolyEthylene (HMPE) ropes, like those in the Acera series, represent the next generation of rope technology.
- Weight Considerations: HMPE ropes are significantly lighter—up to 80% less than steel wire ropes of equivalent strength. This reduces the overall weight of equipment and structures.
- Strength and Performance: Despite their lightweight nature, HMPE ropes match or even exceed the tensile strength of traditional steel ropes.
- Flexibility and Handling: HMPE ropes are more flexible, making them easier to handle, splice, and store.
Benefits of Advanced Ropes
- Safety Enhancements: Lighter ropes reduce the physical strain on workers, decreasing the risk of injuries during installation and maintenance.
- Corrosion Resistance: HMPE ropes are impervious to rust and resistant to many chemicals, ideal for marine and industrial environments.
- Fatigue Resistance: They exhibit superior fatigue performance in cyclic bending situations over steel ropes.
However, steel wire ropes still hold an advantage in certain high-temperature applications and situations requiring minimal elongation. Italian manufacturers produce both types, ensuring that clients receive the best product for their specific needs.
Production and Quality Standards for Wire Ropes
Manufacturing Processes in Italy
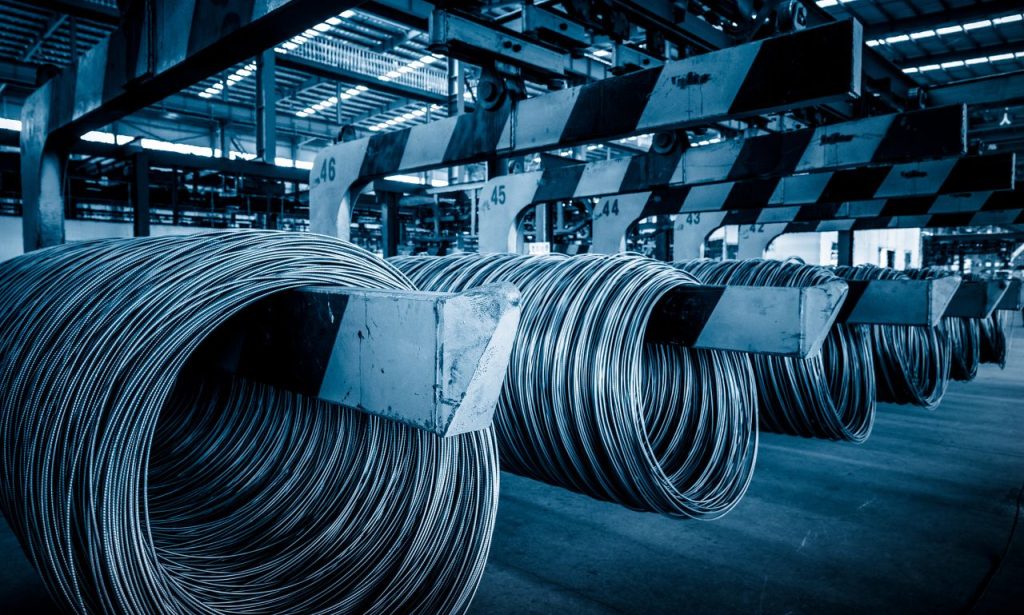
Italy’s reputation in wire rope manufacturing is built on a combination of traditional craftsmanship and cutting-edge technology.
- Raw Material Selection: High-quality steel is the foundation. Manufacturers source premium-grade materials to ensure the final product’s integrity.
- Precision Engineering: Advanced machinery and control systems ensure that the wires are drawn, stranded, and closed with exacting precision.
- Skilled Workforce: Italian artisans bring generations of expertise, ensuring that every rope meets stringent quality benchmarks.
Adherence to Safety Regulations
Compliance with international safety standards is non-negotiable.
- ISO Standards: Italian wire ropes adhere to ISO 2408 for general purpose wire ropes and other relevant standards for specialized applications.
- Testing Protocols: Ropes undergo tensile testing, fatigue testing, and non-destructive examinations to detect flaws.
- Certifications: Many Italian manufacturers hold certifications from recognized bodies like DNV GL, Lloyd’s Register, and others, attesting to their quality management systems and product standards.
When you choose a steel wire rope from Italy, you’re investing in a product that meets the highest global standards, backed by certifications and a commitment to excellence.
Innovative Engineering in Wire Rope Design
Recent Advancements
The wire rope industry is constantly evolving, with Italian innovators leading the charge.
- Coating Technologies: New coatings, such as zinc-aluminum alloys, offer better corrosion resistance than traditional galvanization.
- Embedded Sensors: Smart ropes with built-in sensors can monitor tension, temperature, and wear in real-time, providing valuable data for maintenance and safety.
- Material Innovations: The development of ultra-high-strength steels and hybrid ropes combining steel and synthetic fibers enhances performance characteristics.
Impact on Performance and Longevity
These advancements translate into tangible benefits.
- Increased Uptime: Enhanced durability means less frequent replacements and lower downtime for equipment.
- Predictive Maintenance: Sensor-equipped ropes allow for proactive maintenance schedules, reducing the risk of unexpected failures.
- Cost Efficiency: Although advanced ropes may have a higher initial cost, their extended lifespan and reduced maintenance needs offer better value over time.
Italian engineering not only improves the performance of wire ropes but also contributes to safer and more efficient industrial operations worldwide.
Maintenance and Inspection of Wire Ropes
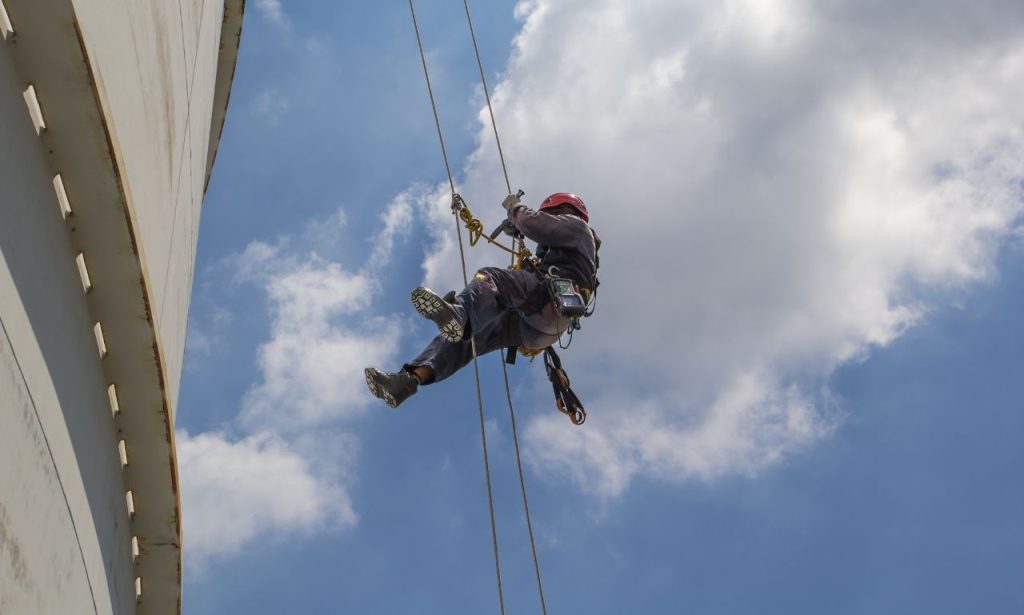
Best Practices
To maximize the lifespan and safety of wire ropes:
- Regular Inspections: Conduct visual inspections before each use and detailed inspections at regular intervals, checking for signs of wear, corrosion, and damage.
- Proper Handling: Avoid dragging ropes over sharp edges or rough surfaces. Use sheaves and drums of appropriate size to prevent undue stress.
- Cleanliness: Keep ropes clean from dirt, debris, and chemicals that can accelerate wear and corrosion.
- Record Keeping: Maintain logs of rope usage, inspections, and any incidents. This data helps in making informed decisions about replacements.
Signs of Wear and Tear
Early detection of issues can prevent accidents.
- Broken Wires: A certain number of broken wires in a given length is a sign that the rope should be retired.
- Corrosion: Pitting, rust, or discoloration indicates that the rope’s integrity is compromised.
- Deformations: Kinks, birdcaging (unraveling of strands), or flattened areas are serious defects.
- Diameter Reduction: A decrease in rope diameter can signal internal wear or core deterioration.
Regular maintenance ensures that your investment in a high-quality steel wire rope from Italy delivers the maximum return in terms of performance and safety.
Isn’t it time you partnered with a supplier that delivers on quality, safety, and innovation? Elevate your operations by choosing steel wire rope from Italy—where engineering excellence meets unmatched reliability. Make the smart choice today and secure the future of your projects with the best in the business.
FAQs
A: The lifespan varies depending on usage, maintenance, and environmental factors. Regular inspections and proper care can significantly extend its life.
A: Common steel grades include improved plow steel, extra improved plow steel, and bridge rope. Each grade offers different strength and durability characteristics.
A: Look for certifications, industry affiliations, and customer testimonials. A reputable supplier will be transparent about their manufacturing processes and quality control measures.
A: Always wear appropriate personal protective equipment (PPE), inspect the rope before each use, and follow safe lifting practices.